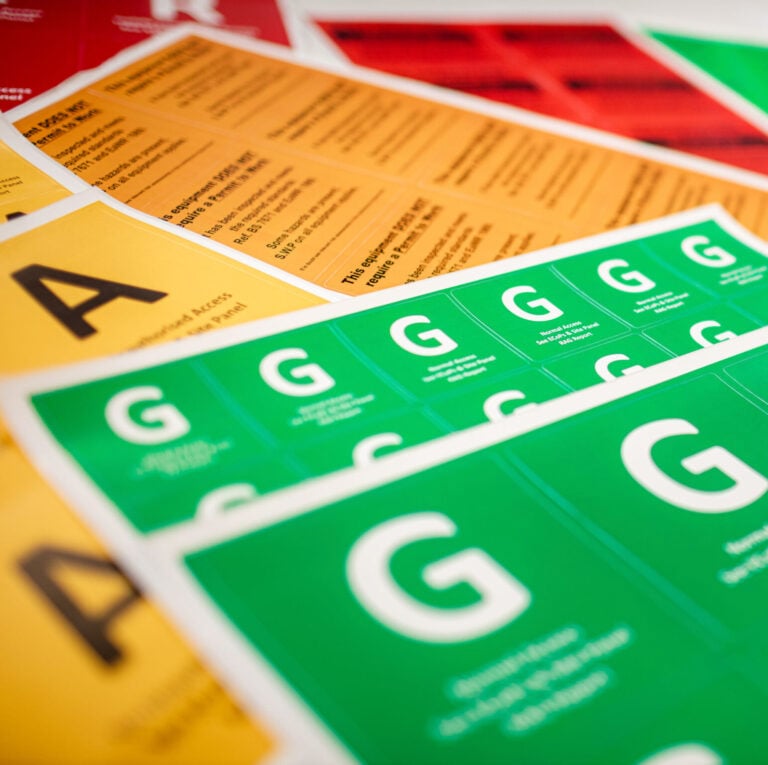
Panel Risk Assessment
The Electricity at Work Regulations 1989 under Regs 4 (1) & (2) prescribe that: ‘As may be necessary to prevent danger, all systems, shall at all times be of such construction, so as not to give rise to danger’.
Furthermore, paragraph 69 of EaWR 1989 states that: ‘Records of maintenance, including test results, preferably kept throughout the working life of an electrical system will enable the condition of the equipment and the effectiveness of maintenance policies to be monitored’.
Under the Health and Safety at Work Act 1974 you have to ensure, so far as reasonably practicable, the health and safety of yourself and others who may be affected by what you do or do not do. It applies to all work activities and premises and everyone at work has responsibilities under it. The Management of Health and Safety at Work Regulations 1999 also apply to every work activity and workplace and require all risks to be assessed and, where necessary, controlled
Maintaining a safe system of work and storing actual records of maintenance relative to both panel entry and working in panels, in our experience, is often excluded from clients’ maintenance schedules, leaving Duty Holders unwittingly exposed under EaWR 1989 should there be a breach of the regulations.
Guardian Electrical Compliance Ltd has been aware of the foregoing situation for some time and whilst responding to and fulfilling client requests to provide a solution, it is only recently, together with the assistance of the Tesco Maintenance Team and the flexibility of TraQit, that the solution has been developed and proven in the field.
Duty Holder – Ask yourself the following questions...
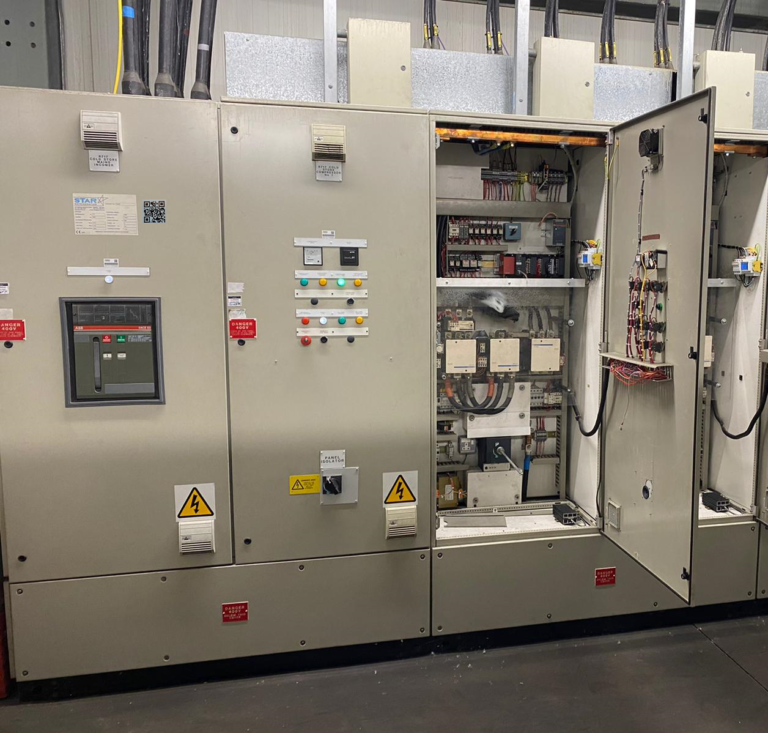
- Do you have a Safe System of Work for Panel Entry that is continually monitored, recorded and archived? (For example: main & sub panels, HVAC & control panels, and DBs.)
- Does the Safe System of Work incorporate the level of competence required for panel entry?
- Do you use approve sub-contract maintenance providers and do you check their check their competence to work in plant or process control panels?
- Is there an obvious visible red, amber, green labelling standard for panel entry?
- If so, is the status clearly defined and instruction provided to internal and external maintenance teams on safe entry procedures?
- Is there a clear identification/numbering system supported by current schematic drawings?
- Are isolators provided and in good working order, are they interlocked with panel doors or have they been defeated in order to enable access without isolating equipment for maintenance purposes?
- Are components within equipment IP2X rating compliant, or are exposed live parts present with covers/doors open or removed?
- Are you satisfied you are in control of the Panel entry/maintenance process?